Precision Metal Fabrication
Precision is vital in metal fabrication—it helps manufacturers turn block or sheet materials into custom parts for machines, structures, and other products. Precision metal fabrication frequently deals with components and parts used in high-tech machinery.
Now that technologies like computer numerical control (CNC) are available, manufacturers can make components that are virtual twins to the original in terms of design and durability. These processes take precision metal fabrication to another level. Consequently, the machining market is estimated to be more than USD 400 billion worldwide.
Many industries depend on precision metal fabrication, like the following:
- Electronics and communication;
- Transportation (seafaring vessels, bus, rail, automotive, and aviation;)
- Agriculture;
- Medical equipment/devices;
- Energy;
- Food and beverage;
- Construction;
- Commercial and consumer goods.
- Architecture.
Precision metal fabrication is used for various materials, including sheet metal. Sheet metals used in precision fabrication can produce detailed and complex metal parts in all shapes and sizes used in machinery and other equipment in many industries.
Precision Metal Fabrication Benefits
Gone are the days when blades, hammers, and other manual implements are used to fabricate components. Nowadays, if you want metal parts cut to exact specifications, high-tech processes like CNC are used. Techs like this employ focused, powerful laser beams to create highly accurate metal components.
Lasers are beneficial for cutting tiny holes and making intricate designs and custom shapes. If you want to try using a laser for your metal fabrication project, here are some laser cutting tips.
For many industries, precision metal fabrication is essential to their business. Below are a few reasons why:
Getting Costs Down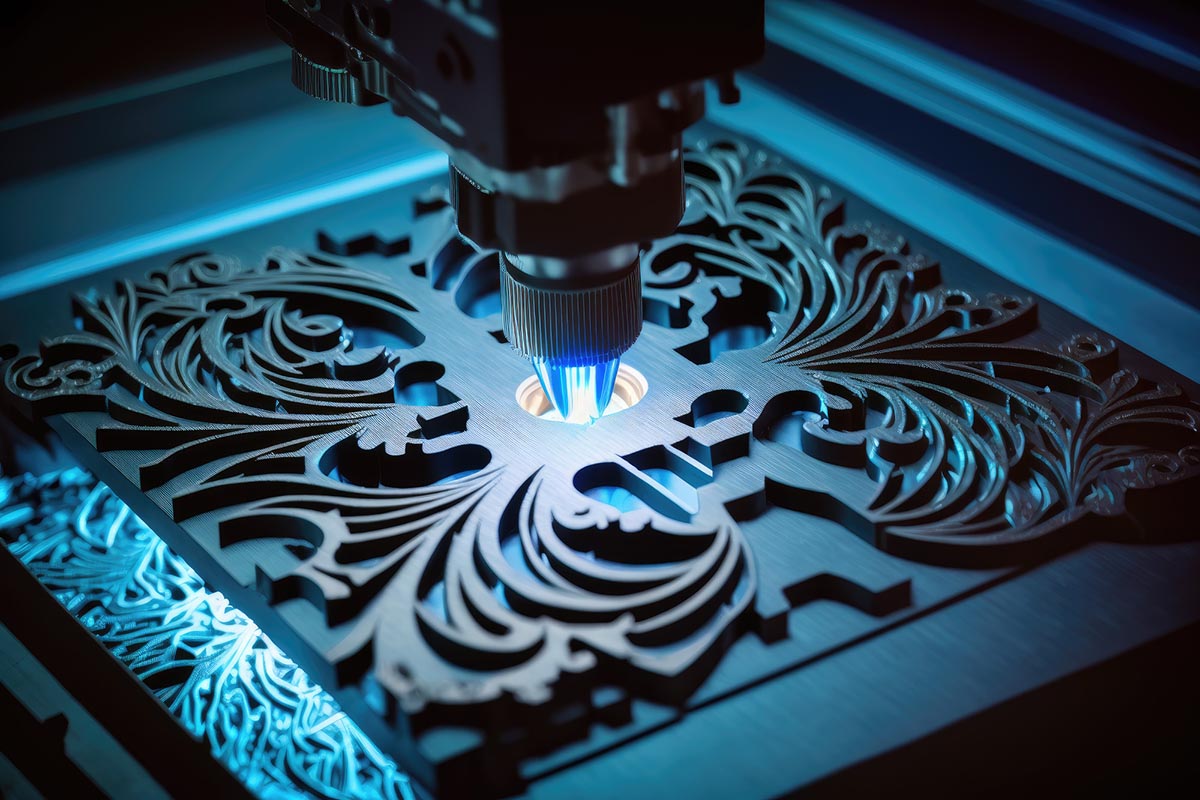
Custom-made components with tight tolerance, meaning the accuracy and precision needed for producing a part, continue to be in demand across all industries. However, relying on conventional machining techniques to meet these tolerances can cost an arm and a leg.
Precision metal fabrication with lasers for complex and custom parts costs less. Moreover, technologies like these mean savings on labor expenses. You won’t have to deal with casting or molding methods typically involved in conventional techniques to produce the same result.
Moreover, you can do it without investing in costly specialized tools and machinery. In a product development cycle, this process can be invaluable, not only in terms of money but also in terms of time saved.
Precision metal fabrication produces tight-tolerance components at a lower cost than conventional methods.
Fast Fabrication
Speed is a critical element in many industries. And when it comes to machining processes, precision manufacturing is the speediest compared to other methods. The reason is that conventional fabrications rely on human control. Precision manufacturing, on the other hand, has computer-based controls, like specialized software and computer-aided design (CAD) models.
Using this process, you can manufacture parts and components in days. Other methods would most likely take weeks or sometimes months to produce the parts you want. This process means you’ll have speedy fabrication, no human errors, and consistent and accurate products.
Consistency
Precision fabrication processes are also known for producing consistent parts. Consistency is vital because errors and inaccuracies in manufacturing are often the results of variables. As these variables are outside the manufacturer’s control parameters, they’re often the culprit in producing inconsistencies that affect quality.
Processes that result in too many variables mean increased errors. On the other hand, using a method that results in fewer variables means maintaining first-rate products is much easier. If there’s an error, diagnosing its cause is more straightforward.
In precision metal fabrication, the component’s design is created using tools like CAD. The drawing of the part is stored afterward on the system as a file.
This drawing is the blueprint, which provides the exact specifications for the process. Subsequent fabrication runs will use this original drawing as the blueprint to produce the component conforming to the initial measurements consistently.
Improved Quality
Improved quality of manufactured products is another vital benefit of precision fabrication. Techs like CNC and other computer-based precision tools significantly increase accuracy when creating parts to exact specifications. For delicate and intricate components, accurate measurements and tight tolerances are crucial.
Precision metal fabrication is head and shoulders above manual casting or fabrication about quality. Consequently, the final products have fewer defects, resulting in repair savings. Parts and components that perfectly fit when assembled increase quality, efficiency, and performance.
Versatility
Another crucial benefit of precision metal fabrication is its versatility. The flexibility and adaptability the process brings to the table allow manufacturers to fabricate high-quality custom parts quickly and efficiently. This ability lets you easily adjust your tools to manufacture new components from scratch if needed.
And if you need to modify an existing one, you can do that quickly, too. Moreover, precision metal fabrication can easily make a viable product prototype for a client looking to produce a prototype of their concept.
Conclusion
Many industries increasingly rely on the precision metal fabrication to produce complex and custom components. The process gives several benefits to manufacturers and clients alike. Creating parts with tight tolerances, for example, is cheaper.
Manufacturing custom parts is also faster with precision fabrication compared to conventional methods. The process produces consistent and high-quality products. It’s also versatile—you can quickly adapt your tools to make new products or modify an existing product. Fabricating a workable prototype quickly is also possible.